The differences between purely handmade violins and handmade violins
Many violins are divided into many types. There are purely handmade violins, some are called handmade violins, and there are also factory violins and machine violins. There are various names. So today we will mainly talk about two types that people often confuse, that is, purely handmade violins. The comparison and difference between violins and handmade violins, the following is what I want to tell you today.
欢迎选购艺匠琴坊的弦乐器,您可以点击此链接与我们建立联系!
What is the difference between a purely handmade violin and a handmade violin?
The biggest difference between handmade and artisanal is the way they are made. A handmade violin is entirely made by hand, including the carving, polishing and assembly of every part. In contrast, a handmade violin may use machines to make some of its parts, and may use cheaper materials.
In addition, the two types also differ in the following ways:
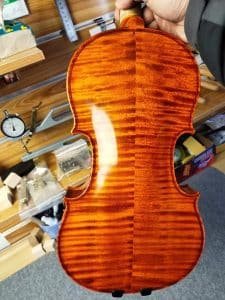
1. Material selection
Purely handmade violins require the use of high-quality materials, such as rare woods and high-quality strings. These materials cost more and need to be carefully selected and processed to ensure the violin has the best sound and appearance quality. In handmade violins, some cheap materials may be used to reduce costs.
2. Production process
Purely handmade violins require multiple steps, including material selection, design, engraving, assembly and adjustment. Each step requires meticulous technique and experience to ensure the violin sounds and looks its best. In contrast, handmade violins use machines to help create some of the components and may lack some detail and precision.
3. Price difference
Because handmade violins take more time and skill to make and use high-quality materials, they are generally more expensive than handmade violins. Handmade violins may be more suitable for musicians on a budget or beginners.
The production process of a purely handmade violin
The production process of a handmade violin is very complex and requires a high degree of skill and experience. The following is the general production process:
1. Material selection
The most important material for a handmade violin is wood. Violins are usually made of pine or maple, with pine used for the top, bottom and sides, and maple used for the neck and fingerboard. These woods need to be carefully selected and treated to ensure they have the desired sound and density.
2. Make the main body of the violin
Making the body of a violin requires the use of a variety of tools and techniques. First, the wood is cut into the desired shape and size; then, they are glued together and carved and sanded using scrapers and planes. Next, the neck, fingerboard and other details of the violin need to be similarly treated.
3. Accessories for assembling the violin
After the main body of the violin is completed, accessories need to be installed, including tuning pins, tail hooks, string seats and tail cloths. These accessories require careful adjustment and installation to ensure that they match the quality and sound quality of the violin body.
欢迎选购艺匠琴坊的弦乐器,您可以点击此链接与我们建立联系!
Trimming and tuning the violin
Ultimately, the process of making a handmade violin is not about putting all the components together, but rather a series of meticulous adjustments and finishings. These steps can greatly affect the sound quality and appearance of your violin.
1. Adjust the string height
String height refers to the distance between the bow and the fingerboard. If the string height is too low, the violin will make noise and buzz. And if the string height is too high, it will make the player feel difficult. Therefore, it is very important to adjust the string height according to the needs of the player and the characteristics of the violin.
2. Adjust the tuning pin
The peg is the part on the violin that adjusts the string tension. They need to be installed and adjusted correctly to maintain stable tension in the strings and provide the player with the best playing experience.
3. Repair the bridge
The bridge is the key component that connects the violin strings to the resonance box. It needs to be precisely carved into a suitable shape to ensure that the length, angle and tension of the string are all correct. Once adjusted, the bridge needs to be adjusted by adjusting the tuning pins to ensure that it matches the position of the inside wall of the resonance box.
4. Optimize the bow
Optimizing the bow is also an important step in tuning your violin. Bows need to be trimmed to the proper shape, length, and weight to enable the player to obtain the best sound quality and playing experience.
5. Processing the resonance box
The resonance box is one of the most important parts inside the violin. It needs to be designed to a suitable size and shape, and trimmed internally to produce the best possible sound. Machining the resonance box requires very careful work, as even small changes can have a big impact on the sound of the violin.
difference in price
Because handmade violins take more time and skill to make and use high-quality materials, they are generally more expensive than machine-made violins. The price of a pure handmade violin usually ranges from a few thousand to hundreds of thousands of dollars, while a handmade violin usually ranges from a few hundred to a few thousand dollars. This means that pure handmade violins may only be owned by advanced musicians or wealthy collectors, while handmade violins are more suitable for musicians with a limited budget or beginners.
in conclusion
The difference between a handmade violin and a handmade violin is the quality of construction and choice of materials. Purely handmade violins usually have higher sound and appearance quality, and are more expensive. A handmade violin may be more suitable for musicians on a budget or for beginners. When choosing a violin, you need to consider your personal needs and budget to make the best choice. Regardless of the type of violin, they require careful adjustment and trimming to achieve the best sound quality and playing experience.